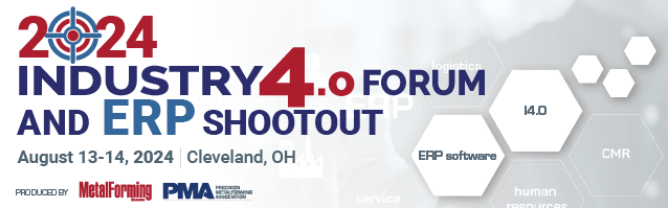
MetalForming magazine and the Precision Metalforming Association are excited to host an informative forum on Industry 4.0 applications for metal formers and fabricators, and a tour of some of the industry’s leading ERP software systems.
Day one features presentations on Industry 4.0 applications and a networking reception with attendees, speakers and sponsors. Day two features shootout sessions that provide attendees with an in-depth software demonstration from four leading suppliers, and users will participate in lively group discussions designed to address any questions regarding software features and functionality.
Topics to be covered:
- AI That Makes Sense for Metal Formers
- The Shopfloor Data You Need to Measure
- ERP: Managing Change
- Tips for ERP Vendor Selection
- Planning the Next ERP Implementation Project
August 13th & 14th at PMA’s HQ in Independence, OH
Who Should Attend?
The event is designed for executives, engineers and IT professionals working in small to midsized manufacturing companies.
Featured Speaker: Bryan Sapot, CEO of Mingo Smart Factory
Topic: Increasing Overall Equipment Effectiveness Starts with Change Management
Knowing why overall equipment effectiveness (OEE) increases is just as important as why it decreases. Manufacturing analytics and a visual representation of the factory floor work together to identify areas of improvement. Change doesn’t just happen through the data though, it takes a shift in management to use these insights to make actionable decisions. Mingo Smart Factory has worked with hundreds of manufacturers to discover seven fool proof ways to increase OEE. Communication, scoreboards, collecting pertinent data and a commitment to continuous improvement are the key to improving OEE.
How OEE Software Enhances Operational Efficiency
By continuously monitoring key metrics such as availability, performance, and quality, businesses can proactively identify issues and take corrective actions promptly. This proactive approach minimizes downtime, reduces waste, and improves overall equipment effectiveness.
For example, imagine a manufacturing plant that utilizes OEE software to monitor its production line. The software tracks the availability of each machine, the speed at which they operate, and the quality of the output. If a machine experiences a sudden drop in performance, the software immediately alerts the maintenance team, allowing them to address the issue before it leads to a complete breakdown. This proactive maintenance approach not only saves time and resources but also ensures uninterrupted production.
Furthermore, OEE software enables businesses to analyze historical data and identify patterns or recurring issues that may hinder efficiency. By understanding the root causes of inefficiencies, organizations can implement targeted improvements and optimize their operations. This continuous improvement cycle helps businesses achieve higher levels of operational efficiency over time.