Welcome to an exploration of manufacturing productivity – a deep dive into the trends and best practices.
This benchmark report aims to shed light on where the industry stands, what challenges it faces, and how forward-thinking companies are leveraging technology to create leaner, more efficient operations.
Manufacturing productivity is an essential facet of any industry. It’s a measure of a company’s efficiency, assessing how effectively inputs, such as labor and materials, are converted into outputs or finished goods.
A high level of productivity is synonymous with optimized processes, reduced waste, and increased profitability.
In recent years, the manufacturing sector has experienced a paradigm shift.
With the advent of Industry 4.0, also known as the fourth industrial revolution, technologies such as AI, machine learning, IoT, and smart factory solutions have made their way into production lines around the globe.
We hope this report will provide valuable insights to help you understand and navigate the ever-evolving landscape of manufacturing productivity.
Trends and Best Practices in Manufacturing Productivity
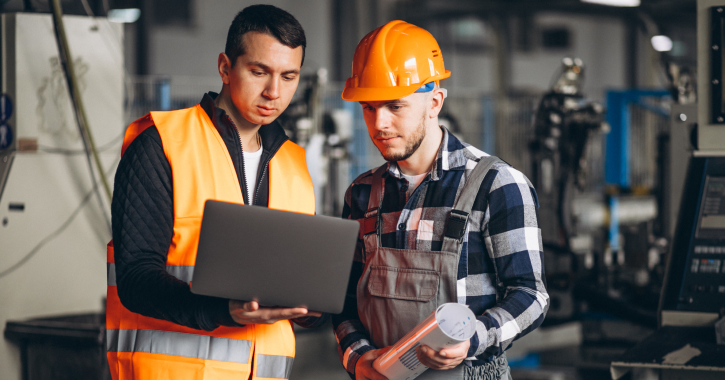
Manufacturing productivity is a dynamic field, constantly being reshaped and redefined by emerging trends, innovative technologies, and best practices.
The following sections delve into the significance of manufacturing productivity and the key factors that influence it.
Importance of Manufacturing Productivity
In the world of manufacturing, productivity is more than just a metric – it’s a vital determinant of a company’s business performance, competitiveness, profitability, and long-term sustainability.
High productivity means maximum output with minimum input, leading to cost efficiency and a healthier bottom line. Moreover, it’s a direct reflection of how well a company utilizes its resources, including labor, materials, and equipment.
It’s essentially one of the crucial key performance indicators that provide insight into the company’s manufacturing performance.
But productivity has impacts beyond the factory floor. It shapes the quality of products, affects delivery timelines, and influences customer satisfaction.
Good project management practices can enhance productivity by ensuring smooth workflows and minimizing unplanned machine downtime.
It also plays a critical role in job creation and economic growth. As companies become more productive, they can expand operations, hire more staff, and contribute more to the economy.
Hence, manufacturing productivity is not just an internal company matter; it’s a concern of wider societal relevance.
Key Factors Influencing Manufacturing Productivity
A myriad of factors influences manufacturing productivity. Here, we’ll discuss four key elements: technology adoption, process optimization, employee engagement, and data management.
Technology Adoption
The adoption of advanced technology is a significant driver of manufacturing productivity. From automated assembly lines to AI-powered predictive maintenance, technology is helping manufacturers ramp up production, reduce errors, and streamline operations.
For instance, smart factory solutions like Mingo Smart Factory provide real-time visibility into production processes, alerting managers to issues before they cause significant downtime.
Technologies such as IoT, AI, robotics, and data analytics are no longer futuristic concepts but essential tools for modern manufacturers.
Process Optimization
Process optimization involves refining manufacturing procedures to eliminate waste, reduce downtime, and increase efficiency.
This can be achieved through various strategies, including Lean manufacturing, Six Sigma, and Kaizen. These methodologies focus on continuous improvement, emphasizing the importance of regularly reviewing and refining processes to improve productivity.
Employee Engagement
Employees who are engaged tend to be more driven, productive, and dedicated to their tasks. They take pride in their roles, leading to higher-quality output and fewer mistakes.
Employee engagement can be fostered through transparent communication, recognition and rewards, opportunities for growth, and a positive workplace culture.
Moreover, involving employees in decision-making processes can provide valuable insights for improvement, as they’re often the ones best placed to identify inefficiencies in the production line.
Data Management
In the era of big data, effective data management is crucial. Accurate, timely data can inform decision-making, identify inefficiencies, and predict trends.
However, managing and making sense of vast amounts of data can be challenging. This is where automated data collection and analytics come in. By automating data collection and using advanced analytics tools, manufacturers can gain valuable insights, make informed decisions, and ultimately boost productivity.
Manufacturing productivity is influenced by a range of interconnected factors. By staying abreast of trends, adopting best practices, and leveraging advanced technology, manufacturers can stay competitive, improve productivity, and drive business success.
Best Practices in Manufacturing Productivity
The manufacturing industry is filled with a host of strategies and methodologies aimed at enhancing productivity.
Here, we’ll delve into four prominent ones: Lean Manufacturing, Six Sigma, Industry 4.0, and Total Quality Management.
Lean Manufacturing
Lean manufacturing is a productivity-enhancing approach that focuses on reducing waste while maintaining or improving product quality.
It’s centered around the concept of “value,” and any process that doesn’t add value to the final product is considered waste. This methodology can apply to everything from design and production to distribution and customer service.
Lean manufacturing involves several key principles, including:
- Just-In-Time (JIT) production: This approach aims to minimize inventory by producing only what is needed and when it’s needed.
- Continuous Improvement (Kaizen): Employees at all levels are encouraged to suggest ways to improve processes, leading to continual, incremental enhancements.
- Value Stream Mapping: This is a tool for visualizing the entire production process, helping identify sources of waste.
Six Sigma
Six Sigma is a data-driven methodology aimed at improving productivity by reducing the likelihood of error in manufacturing processes.
The objective is to reach a defect rate of fewer than 3.4 per million opportunities – that’s where the term “Six Sigma” comes from, representing six standard deviations from the mean in a normal distribution.
Six Sigma involves two key methodologies: DMAIC (Define, Measure, Analyze, Improve, Control) for improving existing processes and DMADV (Define, Measure, Analyze, Design, Verify) for creating new processes or products.
Industry 4.0
Industry 4.0, also known as the Fourth Industrial Revolution, is the integration of digital technologies into the manufacturing sector. It encompasses technologies like the Internet of Things (IoT), artificial intelligence (AI), cloud computing, and big data analytics.
Industry 4.0 enables “smart factories,” where machinery and systems can communicate in real-time, enabling unparalleled levels of automation and self-optimization.
This leads to greater operational efficiency, flexibility, and productivity. Mingo Smart Factory is an example of a solution that embodies the principles of Industry 4.0.
Total Quality Management (TQM)
TQM is a management approach that seeks to instill a sense of quality consciousness at all levels of an organization.
The main goal is to improve the quality of products and services continuously, thereby enhancing customer satisfaction and productivity.
TQM encompasses a range of strategies, including employee involvement, a process-centered approach, an integrated system, a strategic and systematic approach, continual improvement, fact-based decision-making, and communications.
It emphasizes the involvement of all members of an organization in improving processes, products, services, and workplace culture.
Each of these methodologies and practices offers its own unique approach to enhancing manufacturing productivity.
By understanding and implementing them appropriately, manufacturers can drive significant improvements in their operations, leading to higher productivity, greater efficiency, and increased profitability.
Mingo Smart Factory Users Insights
Mingo Smart Factory is a digital solution that transcends boundaries, serving a diverse range of manufacturing businesses worldwide. The users range from small, single-machine operations to large, multi-site enterprises.
They represent various industries, including automotive, food & beverage, plastic packaging, and more. The platform has been adopted across various roles within these organizations, from shop floor operators to upper management, proving its versatility and user-friendly nature.
Every user story is unique. However, they all share a common goal – to drive manufacturing efficiency and productivity while navigating the ever-evolving landscape of industry trends and technologies.
Mingo Smart Factory has been an integral part of their journey towards achieving these objectives.
Key Benefits Experienced by Users
Improved Machine Performance
Mingo Smart Factory’s platform provides real-time visibility into machine operations, enabling users to identify bottlenecks, downtime, and inefficiencies promptly.
This insight allows for quick resolution of issues, leading to increased machine uptime, efficiency, and overall productivity.
Increased Employee Engagement
Employee engagement is a crucial factor in manufacturing productivity, and Mingo Smart Factory has proven instrumental in this regard.
It also simplifies complex data and presents it in an easily digestible format, empowering employees at all levels to make data-driven decisions.
This involvement not only fosters a culture of continuous improvement but also enhances job satisfaction and motivation among the workforce.
Better Data Management
Mingo Smart Factory transforms this challenge into an opportunity.
The platform automates data collection, eliminating manual errors and saving valuable time.
It also provides powerful analytics tools, converting raw data into actionable insights that drive informed decision-making.
Optimized Production Scheduling
With Mingo Smart Factory, users can streamline their scheduling processes, accurately predict production timelines, and effectively allocate resources.
This leads to improved on-time delivery rates, increased customer satisfaction, and, ultimately, a healthier bottom line.
While these benefits are substantial, they’re just the tip of the iceberg.
Every manufacturing operation is unique, and the true value of Mingo Smart Factory lies in its adaptability to meet specific needs, enabling each user to experience its own set of advantages.
User Success Stories
Let’s take a look at two of our users’ experiences, H&T Waterbury and Lyons Blow Molding.
H&T Waterbury
H&T Waterbury, known for its high-volume, high-speed operations, faced a significant challenge with micro stoppages. These small, unplanned downtime events were causing scrap, unplanned overtime, and increased costs.
Mingo Smart Factory helped H&T reduce micro stoppages by an impressive 71%, eliminating 18 hours of downtime.
How did this happen? By transitioning from manual data entry to Mingo Smart Factory’s automatic data collection, H&T eliminated opportunities for mistakes, and the team could find, diagnose, and solve problems quickly.
The visibility provided by Mingo Smart Factory’s daily and weekly production reports created a culture of communication and teamwork, engaging everyone from the shop floor to management.
With real-time, tangible data, H&T could implement corrective action to fix production problems, monitor their effectiveness, and drive continuous improvement.
Lyons Blow Molding
Lyons Blow Molding, a subsidiary of C.L. Smith, faced issues with mistakes, data accuracy, and non-value-added work.
With Mingo Smart Factory, they experienced improved accuracy and automated reporting, reducing errors and enhancing data reliability.
The Mingo Factory Smart system allowed Lyons to monitor critical elements in their manufacturing process, like temperature, pressures, and timers, thus ensuring the product met quality specifications.
Mingo Smart Factory’s alarm feature proved particularly helpful, alerting the team if a process parameter exceeded the established range.
Furthermore, Mingo Smart Factory brought a significant change in the plant’s labeling system. Instead of manual labeling, which was prone to errors, Mingo Smart Factory integrated with the plant’s labeling software, ensuring accuracy and traceability.
The product line, the time printed, and the unit number were all accurately recorded, eliminating issues related to label mismanagement, incorrect labeling, and mixed load issues.
Dave Aquilina from Lyons Blow Molding said, “It gives us good traceability… We no longer have to worry about label mismanagement on the floor, incorrectly labeled products, or mixed load issues. This has improved accuracy and reduced mistakes.”
Moreover, Mingo Smart Factory helped Lyons automate and integrate their scheduling system, further reducing manual, non-value-added work.
This shift allowed the production supervisors to focus on more valuable tasks, leading to downstream improvements, better inventory numbers, and enhanced customer satisfaction.
Industry Source Insights
Overview
Industry sources are a valuable treasure trove of information, insights, and expert opinions. They range from research reports and white papers to blogs, podcasts, and webinars.
These sources can be from leading market research firms, industry associations, and thought leaders in the field.
They offer a deep understanding of the manufacturing sector, its current state, upcoming trends, and best practices.
For manufacturers, these sources are invaluable.
They offer a wide array of insights and data, from understanding consumer behavior to tracking market trends, analyzing the competitive landscape, and even forecasting future market growth.
Key Findings
Let’s dive deeper into some key findings from industry experts that are shaping the manufacturing sector.
Importance of Data Management in Manufacturing
With the advent of technologies like the Internet of Things (IoT) and artificial intelligence (AI), manufacturers are now able to gather more data than ever before.
But having data is just the first step.
How you manage, analyze, and use this data can make or break your business.
Industry experts emphasize the importance of a robust data management system in manufacturing.
It’s not just about collecting data; it’s about turning that data into actionable insights.
Effective data management can lead to improved operational efficiency, reduced downtime, better product quality, and, ultimately, increased profitability.
Adoption of Industry 4.0
The fourth industrial revolution, or Industry 4.0, is here, and it’s transforming the manufacturing landscape.
It involves the use of digital technologies like IoT, AI, robotics, and cloud computing to create ‘smart factories.’
Experts suggest that manufacturers who adopt Industry 4.0 stand to gain a significant competitive advantage.
It can lead to higher productivity, better product quality, reduced costs, and enhanced customer satisfaction.
It’s no longer a question of if but when manufacturers will fully embrace Industry 4.0.
Employee Engagement and Training
Even though technology is vital in modern manufacturing, it’s the people who truly drive operations. Experts emphasize that employee engagement and training are key to success. Engaged employees bring productivity, innovation, and loyalty. As manufacturing technology advances, ongoing worker training becomes critical to stay efficient. Mingo Smart Factory is excited to be part of this journey, offering solutions that help manufacturers excel in the digital era.
Conclusion
In the ever-evolving world of manufacturing, change is the only constant.
The insights shared above shed light on how innovative solutions, informed by deep insights from users and industry experts, can steer businesses toward gaining a competitive edge through improved productivity, efficiency, and profitability.
We encourage manufacturers to explore, research, and, most importantly, understand how solutions like Mingo Smart Factory could impact their operations.
By embracing these solutions, you can stay ahead of the curve and maintain a competitive benchmarking process to ensure they are at the forefront of industry trends and practices.
Think about the opportunities that can be unlocked by better data management, the benefits of seamless integration with the latest technologies, or the enhanced engagement of your workforce.
These factors contribute to internal benchmarking and drive continuous improvement projects that give your business a distinct advantage.
Reflect on the success stories of H&T Waterbury and Lyons Blow Molding, who found value in the data and were able to drive continuous improvement projects.
In the end, it’s about finding the right tools to boost your productivity, improve your operations, and meet your specific needs.
With its user-centric approach and alignment with industry trends, we believe that Mingo Smart Factory can be a valuable ally in your manufacturing journey.
So, feel free to explore, ask questions, and see if Mingo Smart Factory fits into your vision of an efficient, productive, and future-ready manufacturing operation.
We’re here, ready to join you on your journey to excellence.