Changeover time is the period required to switch a production line from manufacturing one product to another. Effective management of changeover time is crucial as it directly influences overall equipment effectiveness (OEE) and lead time. Shortening this period can significantly improve lead time, allowing manufacturers to meet customer demands more efficiently, reduce inventory levels, and increase production capacity. Properly categorizing and tracking changeover time is essential for accurate OEE calculation and operational improvement.
What is the impact of changeover time on OEE?
Deciding how to categorize changeover can directly affect the availability factor when calculating OEE. If it is directly tied to downtime, then a slow changeover will drag down this number. On the other hand, if it is not tied to downtime, then the OEE number will not change regardless of if changing from one product to the next took five minutes or an hour.
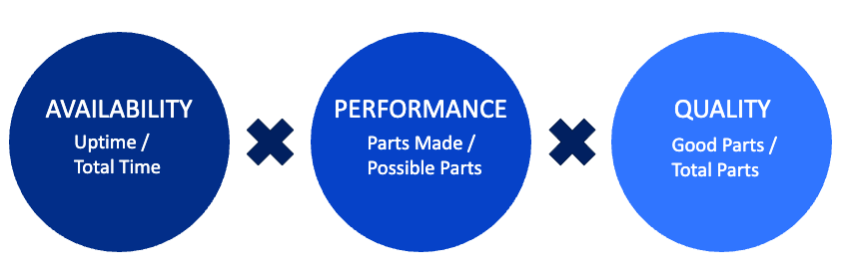
Categorizing Changeover Pros & Cons
When deciding how to categorize changeover time, manufacturers have three main options:
Track as Unplanned Downtime:
Categorizing changeover as unplanned downtime directly affects availability. This is similar to when a line needs to be down for maintenance. The method can negatively effect OEE scores but will help with tracking how long set-up is taking.
- Pros: Provides visibility into the actual time taken for setups, highlighting areas for improvement and motivating operators to reduce changeover time. This approach reduces availability, thus lowering OEE, and emphasizes the need to eliminate or minimize changeover time.
- Cons: It may demotivate operators if the time is perceived as unmanageable, and consistently low OEE can reflect poorly on overall performance metrics.
Track as Planned Downtime:
Not tying changeover to availability is usually a good place to start if you don’t know how long your standard set-up is. It does not impact OEE but can make it difficult to measure.
- Pros: Ensures changeover time does not impact availability or OEE, which can be useful if the standard changeover time is unknown. It prevents penalizing operators for longer changeovers when there is no established benchmark.
- Cons: This approach hides the true impact of changeover time on production efficiency and availability, offering little incentive or visibility into how long the process actually takes.
Hybrid Tracking:
This is the best of both worlds if you already have an idea of how long your standard changeover is.
- Pros: Establishes a benchmark changeover time (e.g., 20-30 minutes) as planned downtime. Any time exceeding this standard is tracked as unplanned downtime. This method provides a clear understanding of how set-up time impacts availability and OEE, offering actionable insights for improvement.
- Cons: Requires an initial effort to determine a realistic standard changeover time, which can vary between processes and products.
Why Option 3 is the Best Approach
Setting a standard changeover time with hybrid tracking is the most effective method for improving changeover time. It combines the benefits of both planned and unplanned tracking, offering a balanced approach. By using real-time data from Mingo Smart Factory’s system, manufacturers can accurately monitor and analyze how long it takes to shift from one product to the next. This system is easy to use, fast to deploy, and provides a quick return on value, making it an ideal tool for enhancing the process.
With Mingo Smart Factory, manufacturers gain real-time insights into changeover durations and can quickly identify deviations from the standard time. This allows for immediate corrective actions and continuous improvement. Operators are motivated to meet the benchmark, knowing that exceeding it will impact availability and OEE, yet they are not unfairly penalized for processes beyond their control. This hybrid approach fosters a culture of accountability and improvement, ultimately reducing changeover time and boosting overall efficiency.
Main Takeaways
- Option 1 – Categorize Changeover as Unplanned Downtime: Highlights setup duration and motivates reduction, but may demotivate if perceived as unmanageable.
- Option 2 – Categorize Changeover as Planned Downtime: Prevents OEE impact without a benchmark, but hides true efficiency and offers little improvement incentive.
- Option 3 – Use Hybrid Tracking: Combines planned and unplanned tracking, providing clear insights and actionable data to improve changeover times.
Using Mingo Smart Factory’s system for real-time data and analysis makes the third option the best choice. This approach not only improves changeover time but also enhances overall production efficiency, providing a significant competitive advantage in the manufacturing industry. Want to see how it works? Schedule a demo today!