In the quest for operational excellence, visibility is key. Starting simple with a single data point can be a powerful and pragmatic first step for manufacturers to gain visibility. By harnessing the power of real-time data and integrating it with production monitoring software, manufacturers can gain invaluable insights into their operations. These insights can pave the way for informed decision-making and continuous improvement.
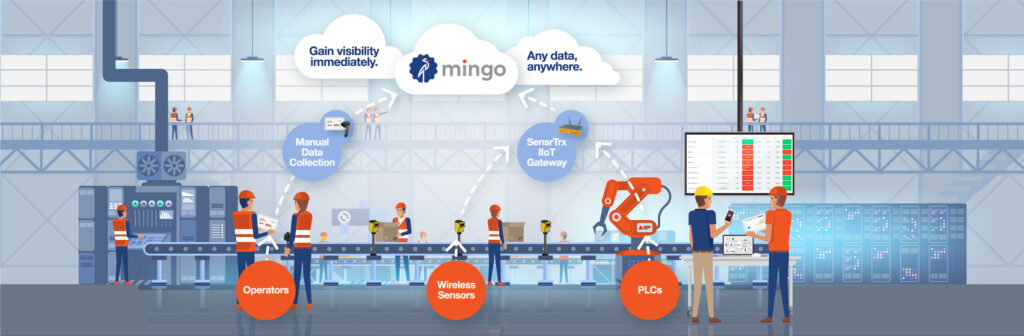
Start Simple with One Data Point
The first step is to identify a single critical data point that provides meaningful insights into the production process. This could be anything from machine uptime and downtime, production output, or quality control metrics. Most of Mingo Smart Factory’s customers start with production counts or downtime. By focusing on a single data point, manufacturers can avoid being overwhelmed and ensure that their efforts are targeted and actionable.
Once a single data point has been identified, manufacturers can target and integrate it into Mingo Smart Factory’s production monitoring software. This software acts as the central hub for capturing, analyzing, and visualizing real-time data from the factory floor. Production monitoring software enables manufacturers to gain a comprehensive view of their operations. For some manufacturers, this may be the first time they have gained visibility into the overall health of their plant. This dashboard is not just limited to the overall flow of the factory floor. It can also focus in on individual lines. The data is aggregated from various sources on the factory floor to an intuitive manufacturing dashboard.
Case Studies
- When H&T Waterbury integrated Mingo Smart Factory with their battery production, they quickly realized that downtime was a much bigger problem than they had originally thought. With the help of Mingo, they were able to reduce their micro stoppages by 71%. Check out the case study.
- Tacony Inc. was able to get control of a 14-week backlog in their West Chicago furniture plant by getting clear metrics within their production process with the help of Mingo. Check out the case study.
- Ice Industries gained accountability and visibility into their plant operations and scrap rates with the help of Mingo Smart Factory. Their count accuracy improved nearly 100%. Check out the case study.
- One of Mingo’s newest customers recently discovered that one of the main sources of their downtime was a line that was consistently waiting for a forklift to deliver materials.
The Power of Real-Time Data in Visibility for the Factory Floor
Starting simple with a single data point opens up a world of possibilities. The benefits of integrating real-time data with production monitoring software are significant. First, it enables manufacturers to identify and address issues in real-time, minimizing downtime and maximizing productivity. For example, if a machine experiences a sudden drop in uptime, production monitoring software can alert operators immediately. This allows them to take corrective action before it escalates into a major problem.
Moreover, real-time data integration facilitates data-driven decision-making, enabling manufacturers to optimize processes, allocate resources more effectively, and improve overall efficiency. By having access to up-to-date information about machine performance, production output, and quality control metrics, decision-makers can make informed decisions that drive continuous improvement and operational excellence.
Next Steps
Perhaps the most exciting aspect of starting simply with a single data point is the expandability of data when performing manufacturing analytics. As manufacturers become more comfortable with collecting and analyzing data, they can gradually expand their scope to include additional data points and metrics. For example, manufacturers can use production monitoring to know why their OEE score goes up or down. This iterative approach allows manufacturers to unlock new insights and opportunities for optimization. The goal is to drive continuous improvement, innovation and lean manufacturing principles across the entire organization.
The Mingo Way: Start Simple, Think Big, Move Fast
Starting simple with a single data point is a powerful strategy for driving operational excellence and visibility. By integrating real-time data with production monitoring software and leveraging the expandability of data when performing manufacturing analytics, manufacturers can gain invaluable insights into their operations, optimize processes, and drive continuous improvement.
Thinking big means having a vision for how you want your business to grow. Start making a list of what else you would like to know once you have addressed the first data point.
Mingo Smart Factory’s production monitoring system is fast to deploy and implement. Start getting quantitative data in days, not weeks.
So why wait? Start your journey to visibility today, one data point at a time. Contact Mingo Smart Factory for a demo today.